Как 3D-печатные слуховые аппараты тихо захватили мир?
Друзья, с момента основания проекта прошло уже 20 лет и мы рады сообщать вам, что сайт, наконец, переехали на новую платформу.
Какое-то время продолжим трудится на общее благо по адресу
На новой платформе мы уделили особое внимание удобству поиска материалов.
Особенно рекомендуем познакомиться с работой рубрикатора.
Спасибо, ждём вас на N-N-N.ru
Автор: Александр Корнвейц. 3D-печать захватила рынок пользовательских слуховых аппаратов. Сегодня почти 100% таких аппаратов печатается на 3D-принтерах. По оценкам, общее количество используемых 3D-печатных слуховых аппаратов составляет более 10 миллионов. Только швейцарская компания Sonova, мировой лидер в области производства решений для улучшения слуха, утверждает, что произвела более 1 000 000 единиц в 2016 году. И похоже эта «революция» осталась без внимания.
Почему вы впервые слышите о 3D-печатных слуховых аппаратах? Чтобы ответить на этот вопрос, нужно вернуться к истокам появления этих замечательных устройств.
Принцип работы слухового аппарата заключается в том, что он улавливает звуки из внешнего мира, а затем усиливает их в ушах слабослышащих людей, по существу, делая эти звуки просто громче. Современные слуховые аппараты бывают разные по форме и дизайну. Но только изготовленные на заказ типа внутриушных In-the-Ear (ITE) и канальных In-the-Canal (ITC) используют технологию 3D-печати. Остальные, включая более распространенные заушные слуховые аппараты (BTE), все еще продолжают производиться традиционным способом.
Изготовленные на заказ 3D-печатные слуховые аппараты моделируются с учетом анатомии уха каждого отдельного пациента. По сравнению с розничными версиями эти пользовательские модели значительно удобнее, их превосходная посадка уменьшает движение или скольжение в ухе. Некоторые из самых маленьких ITC-моделей, особенно те, которые носят глубоко в ушном канале, продаются исключительно как индивидуальные модели.
Как изготавливаются индивидуальные слуховые аппараты?
Первые слуховые аппараты, известные как «слуховые трубы», появились в 17 веке. По форме они представляли собой большой рожок и производились профессиональными мастерами инструментов. Потом появились слуховые аппараты в чемоданчиках. И только после окончания второй мировой войны приборы стали полностью электронными, а большие и коробчатые формы сменились на современные миниатюрные устройства, которые крепятся вокруг уха. Кроме того, они стали мощнее.
Современные слуховые аппараты действуют не только как усилитель звука, но и содержат микропроцессоры, которые могут регулировать собственный уровень звука, громкость, использовать Bluetooth и даже передавать звук с внешних устройств, таких как смартфоны или телевизоры. Слуховые аппараты типа ITE предназначены для размещения главным образов в ушной раковине. При этом динамик и внутренняя электроника помещаются в одном корпусе.
Слуховые аппараты ITC – канальные, располагаются в основном в слуховом канале, и имеют массу преимуществ за счет индивидуальной формы. Модели BTE почти не делаются на заказ, так как не должны соответствовать размерам конкретной ушной раковины и слухового канала. Традиционно их изготавливают так: в слуховой проход пациента вводится силиконовая масса, затем по ее форме отливается форма самого аппарата, техники вручную вставляют другие компоненты, готовый аппарат полируется и тестируется. Несмотря на точность, процесс относительно медленный, а материал дорогой.
Но на помощь пришла 3D-печать.
Процесс создания 3-печатных слуховых аппаратов
Этап 1: Создается силиконовая форма слухового канала.
Этап 2: Вместо создания литьевой формы, как при обычном способе изготовления, оттиск сканируется с помощью 3D-сканера и загружается в специальную компьютерную программу.
Этап 3: Модель оправляется на 3D-принтер и печатается из фотополимерной смолы.
Этап 4: Устанавливаются и тестируются другие компоненты 3D-печатного слухового аппарата.
Весь процесс может быть завершен всего за один день. Это гораздо быстрее традиционного изготовления.
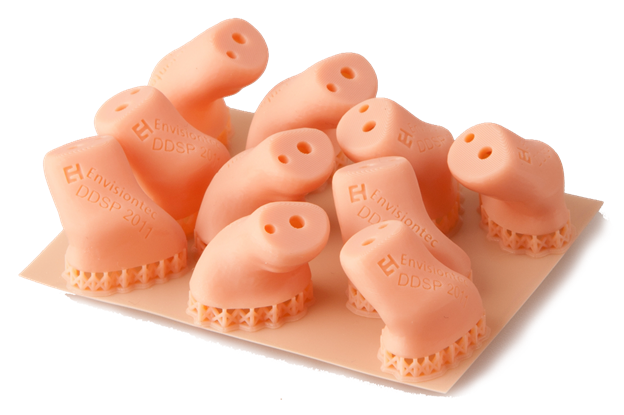
Преимущества 3D печатных слуховых аппаратов
С помощью 3D-печати производство слуховых аппаратов значительно ускоряется. Вместо того, чтобы создавать индивидуальные литьевые формы для каждого оттиска, эти формы теперь можно легко распечатать на 3D-принтере, причем несколько экземпляров печатаются одновременно в одном принтере. В результате можно создать до 50 индивидуальных 3D-печатных слуховых аппаратов в течение часа. Кроме того, они печатаются более точно, меньше времени уходит на финишную сборку.
К сожалению, из-за дороговизны профессиональных 3D-принтеров и материалов для 3D-печати внедрение кастомизированных слуховых аппаратов повсеместно шло медленно. В США стоимость пары таких наушников доходила до 5000 долларов. Мало кто их покупал. 3D-печать в этой области оставалась незамеченной. Примерно 29 миллионов взрослых в США (15% взрослого населения) нуждаются в слуховых аппаратах, однако только каждый третий человек старше 70 лет когда-либо действительно пользовался им. И число таких людей младше 70-ти лет еще ниже.
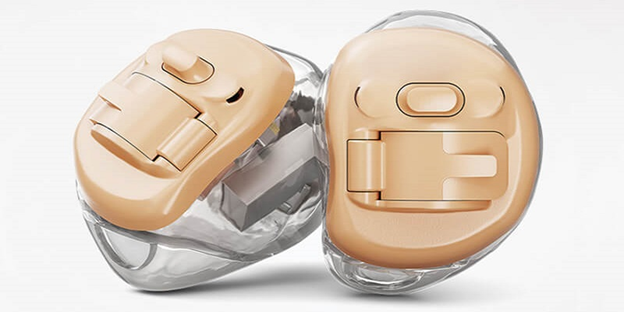
В 2020 году в фотополимерной 3D-печати произошла мини революция, которая была вызвана появлением моно LCD-дисплеев с разрешением 4K. Благодаря им 3D-принтеры стали дешевле, быстрее, точнее и имеют гораздо больший срок службы. Также существенно снизились цены на фотополимерные смолы для 3D-печати. Фотополимерную печать стала доступной, начальные инвестиции снизились с десятков тысяч долларов до сотен. Это сильно облегчило вход в бизнес по по созданию индивидуальных слуховых аппаратов.
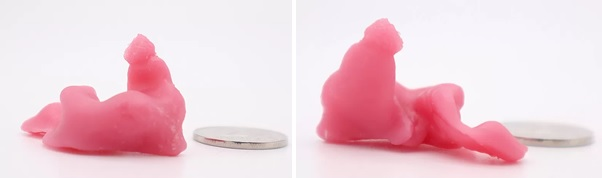
На снимках отпечатанная на бюджетном 3D-принтере Elegoo Mars модель ушной раковины и слухового канала. Цена такого принтера составляет около 20000 рублей, а себестоимость материала не превышает 300 рублей.
Рассмотрим подробнее этапы создания конечного продукта.
Первый этап не отличается от классической методики — происходит снятие слепка. Затем слепок помещается в 3D сканер. При помощи специализированной программы моделирования происходит формирование виртуальной версии будущего изделия. При этом в программе учитываются все особенности рельефа поверхности наружного уха пользователя. Благодаря наглядной визуализации удается максимально оптимизировать размер вкладыша или корпуса слухового аппарата, обеспечивается наилучший косметический эффект без нарушения функциональности.
После завершения моделирования все готово к непосредственной печати изделия. Жидкий фотополимер под воздействием ультрафиолета слой за слоем формирует структуру вкладыша. За один сеанс работы принтера в течении 40–50 минут может быть произведено до 20–25 изделий, что дает высокую производительность и максимально снижает время ожидания готовности индивидуальных моделей пациентами.
После завершения печати корпус и вкладыш проходят финальную обработку, поверхность бережно полируется и покрывается лаком. Наличие виртуальной копии изделия в базе данных позволяет без труда изготовить точную копию корпуса или вкладыша в кратчайшие сроки без необходимости повторного визита пациента.
Из дополнительных преимуществ технологии отметим, что 3D-печать уменьшает количество материала, используемого для создания каждого слухового аппарата. Раньше, когда негативная силиконовая форма была отлита, она уже не могла использоваться повторно, поскольку уникальна для каждого пациента. Хотя 3D-печатные корпуса по-прежнему требуют оттиска ушного канала, отрицательная форма заменяется сканированием оттиска. Таким образом экономятся расходные материалы и снижаются затраты.
Подводя итоги, хочется сказать, что технология 3D-печати идеально подходит для создания кастомизированных слуховых аппаратов. Она дает только плюсы и не несет никаких рисков или потенциальных угроз. Хочется надеяться, что в скором времени эта технология получит повсеместное внедрение, и это поможет многим слабослышащим людям. Сейчас похожая революция происходит в стоматологии и создании протезов. Не за горами и переход в «цифру» отоларингологии.
- Источник(и):
- Войдите на сайт для отправки комментариев