Износостойкие покрытия как движитель инновационного процесса в технологии инструментальных материалов и современной металлообработке
Друзья, с момента основания проекта прошло уже 20 лет и мы рады сообщать вам, что сайт, наконец, переехали на новую платформу.
Какое-то время продолжим трудится на общее благо по адресу
На новой платформе мы уделили особое внимание удобству поиска материалов.
Особенно рекомендуем познакомиться с работой рубрикатора.
Спасибо, ждём вас на N-N-N.ru
В статье дан обзор эволюции технологий нанесения износостойких покрытий для режущего инструмента в приложении к задачам современной металлообработки. Приведена оценка роли отечественных и зарубежных инноваций в этой области. Рассмотрены тенденции развития новых, в том числе и наноструктурированных, типов износостойких покрытий.
История износостойких покрытий
Первые серийные образцы сменных многогранных пластин с износостойкими покрытиями компания Sandvik Cоromant продемонстрировала еще в 1969 году. С тех пор развитие всех инструментальных материалов идет в основном по пути совершенствования методов нанесения покрытий с целью управления их химическим составом, структурой для обеспечения наилучшего сочетания свойств покрытия и основы в различных областях применения.
Покрытия CVD (Сhemical Vapor Deposition)
Первые износостойкие покрытия были получены путем химического процесса осаждения при высоких температурах 950–1050 0C из парогазовой среды. Данный процесс принято сокращенно называть CVD (Сhemical Vapor Deposition). Следует отметить, что данная технология широко применяется не только для нанесения износостойких покрытий на режущем инструменте, но и в других областях техники, где требуется получение слоев покрытия и пленок из кристаллических материалов с высокой чистотой и заданной структурой. Как уже говорилось, процесс СVD для нанесения покрытий на режущий инструмент, был впервые применен компанией Sandvik Coromant (Швеция). Эта фирма в дальнейшем сделала ряд серьезных улучшений первоначальной технологии, как впоследствии в не меньшей мере компании Hertel(Германия), Kennametal Hertel(США), Walter (Германия) и ряд других зарубежных производителей инструмента.
Для Советского Союза и для России технология метода СVD стала доступной благодаря созданию совместных предприятий с двумя первыми фирмами из приведенного списка. Производство Sandvik Coromant, открытое в конце 70х, успешно работает в Москве, по сей день. Однако как на этом, так и на других отечественных инструментальных предприятиях установки CVD используют технологии, основанные в основном на зарубежных разработках.
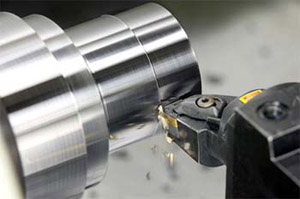
Для улучшения свойств режущего инструмента наибольший интерес представляют покрытия с кристаллической структурой из химически инертных и тугоплавких соединений, таких как карбид титана, нитрид титана, оксид алюминия.
Первые износостойкие CVD покрытия были однослойными с толщиной порядка 4–7 мкм.
Удивительно, что даже довольно примитивное по сегодняшним меркам однослойное покрытие TiC, применявшееся на первых покрытых сменных неперетачиваемых пластинах, дало выраженный эффект в повышении производительности обработки примерно на 50%. Повышение производительности было достигнуто в основном за счет увеличения скоростей резания. Так за десять лет с 1970 по 1980 год скорости резания при снятии основного припуска при токарной обработке возросли в среднем со 100–120 до 150–200 м/мин.

Появление износостойких покрытий совершило революцию в металлообработке еще и потому, что совпало во времени с двумя другими значительными процессами. Так, благодаря износостойким покрытиям, была поставлена точка в развитии инструмента с напайными пластинами. Конструкции инструментов со сменными неперетачиваемыми пластинами показали значительно более высокий потенциал совершенствования, поскольку износостойкое покрытие легко может быть нанесено только на сменную режущую часть, и тем самым сборные инструменты сразу получили решающее конкурентное преимущество. Также в этот период стала активно развиваться автоматизация металлорежущего оборудования на базе ЧПУ. Инструменты со стабильной геометрией режущей части, восстанавливаемой за счет замены режущей кромки поворотной пластины с высокими эксплуатационными характеристиками, полученными от применения износостойких покрытий, были жизненно необходимы для исключения потребности постоянного контроля оператора за процессом обработки. Увеличение стоимости такого автоматизированного оборудования можно было оправдать только одновременным значительным ростом производительности обработки, и износостойкие покрытия оказались наиболее эффективным и сравнительно недорогим методом достижения этой цели.
Выраженный успех первых износостойких CVD покрытий обеспечил их широкое распространение в промышленности, но одновременно выявились существенные ограничения использования инструмента с покрытиями. Наибольшие проблемы вызваны недостаточной адгезией СVD покрытий, а также их негативным влиянием на механические свойства основы. Уровень этого влияния можно пояснить на простом примере. Если взять твердосплавную пластину из обычного сплава с областью применения ISO P30 (умеренная черновая обработка) и нанести простейшее покрытиe CVD, то полученная комбинация уже будет имеет область применения ISO P10–P20. И даже не смотря на то, что диапазон скорости резания для покрытой пластины будет существенно выше, и соответственно выше производительность, ее прочность уже не позволит использовать инструмент для работы в тяжелых условиях. То есть простейшие СVD смещают область применения твердых сплавов в сторону высоких скоростей резания, ухудшая их прочностные характеристики. Учитывая это, можно было бы сделать вывод, что такие сплавы наилучшим образом будут подходить для чистовой обработки, но тут вступает в силу другое ограничение.
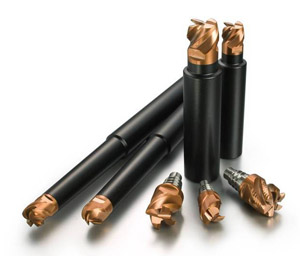
Процесс химического осаждения характеризуется увеличенной скоростью на заострённых участках поверхности изделий. С ростом толщины слоя покрытия адгезия катастрофически снижается. Для инструментальных применений СVD это означает, что толстый и легко откалывающийся слой покрытия ляжет как раз в зоне режущей кромки. С этим можно бороться, значительно округляя режущую кромку перед нанесением покрытия. Минимальная величина округления 20 мкм, типовое значение для современных пластин 35–50 мкм. Подобная подготовка кромки желательна для пластин, предназначенных для черновой и получистовой токарной и фрезерной обработки, но для ряда инструментов кромка должна быть острой. К ним относятся пластины для тонкого финишного точения и расточки, резьбовые и профильные пластины и все типы цельного концевого инструмента. Так для цельных твердосплавных фрез типовая толщина стружки на уровне 20–40 мкм вообще оказывается ниже уровня возможной для СVD остроты кромки, что сравнимо с попыткой аккуратно нарезать колбаску тупой стороной ножа.
Все перечисленные выше недостатки простейших CVD покрытий привели к необходимости серьезных исследований как в области совершенствования технологии CVD, так и в области разработки принципиально иных методов нанесения покрытий. Эволюция СVD покрытий — это более чем 30-летняя история борьбы за устранение противоречия между повышением износостойкости и негативным влиянием на прочность основы, противоречия, заложенного в самой основе высокотемпературного процесса. Тем не менее сейчас можно утверждать, что в результате этой работы большинство проблем было поочередно и весьма оригинально решено, что подтверждается неоспоримым фактом – на протяжении всей истории развития функциональных покрытий режущего инструмента доля метода нанесения СVD и его новых разновидностей превосходит все другие появившиеся позже принципиально иные технологии.
Покрытия PVD (Physical Vapor Deposition) или КИБ (конденсация с ионной бомбардировкой)
Тем не менее во всем мире признается первенство советских, а впоследствии российских разработок в создании второго по объему рынка технологии нанесения покрытий на режущий инструмент, а именно PVD (Phisical Vapor Deposition), или MEVVA (Metal Vapor Vacuum Arc), или КИБ (конденсация с ионной бомбардировкой – термин, применяющийся в русскоязычной литературе). Инструменты с покрытием PVD появились в начале 80х годов прошлого столетия. Идея впервые была реализована в Советском Союзе, но, как это часто бывает, индустриальное применение у зарубежных фирм оказалось более успешным и обширным. Первые покрытия PVD были получены в виде одного слоя нитрида титана TiN толщиной 2–4 мкм. В русскоязычной практике часто встречается название «Булат», закрепившееся как за такими покрытиями с характерным золотистым цветом, так и за установками для их нанесения, получившими определенное распространение на машиностроительных предприятиях СНГ. Популярность нового метода нанесения покрытий определилась в первую очередь тем фактом, что PVD наиболее успешно улучшает свойства тех режущих инструментов, где технология CVD неэффективна или бесполезна. Во-первых, PVD реализуется при принципиально более низких температурах, не превышающих 500 0С, что позволяет покрывать как твердосплавные пластины, так и инструменты из быстрорежущих сталей и даже просто детали машин, работающие в условиях интенсивного трения. Во–вторых, покрытие PVD может быть нанесено на острую кромку и вследствие равномерного характера осаждения не вызывает ее притупления. Таким образом, данный тип покрытий может с успехом использоваться для мелкоразмерных концевых инструментов. В то же время тонкий слой покрытия PVD не может соперничать с более мощными покрытиями СVD, суммарная толщина слоев которых может достигать 22–25 мкм, поэтому по сей день уступает им долю рынка сменных неперетачиваемых пластин.
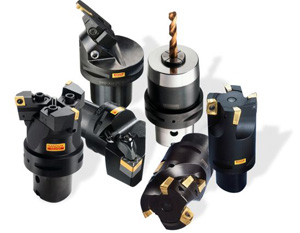
Современные износостойкие инструментальные покрытия, как CVD, так и PVD существенно сложнее первых образцов. Большинство покрытий в настоящий момент выпускаются многослойными с целью создания требуемого уровня защиты инструментальной основы от механических и химических факторов износа за счет комбинации свойств различных частей своей слоистой структуры.
Совершенствование СVD покрытий
Эволюция CVD покрытий шла в трех направлениях. Первое – это снижение негативного влияния покрытия на прочность твердосплавной основы. Второе – улучшение адгезии. Третье – возможность наращивания толщины слоев покрытия для усиления защитных свойств, желательно, не в ущерб двум первым задачам.
Первые попытки поднять защитные свойства покрытий за счет наращивания толщины слоя TiC не дали большого эффекта. Больший эффект был достигнут от внедрения многослойных покрытий СVD, где поверх слоя карбида титана TiC наносились слои оксида алюминия Al2O3 и нитрида титана TiN. При этом первый слой покрытий служил основой для создания хорошей адгезии, а последующие слои усиливали защитные функции от различных факторов износа. Оксид алюминия, как очень простое химическое соединение с высокой химической инертностью и температурной стабильностью, является идеальным компонентом покрытия для зашиты твердого сплава от воздействия высокой температуры и химических видов износа. Кристаллическая форма этого соединения – корунд – давно используется в технике для абразивной обработки. Слои Al2O3 были относительно тонкими – до 4 мкм. Впоследствии с внедрением ускорителей роста стало возможным увеличение толщины слоя до 8–10 мкм.
Твердые сплавы с оксидным покрытием позволили достичь скоростей резания порядка 250–300 м/мин. Сплавы данного типа стали доминировать при чистовой обработке сталей и чугунов. Тем не менее наращивание толщины слоев первых СVD покрытии имело ограниченный успех из-за снижения адгезии и, как следствие, крайне нестабильной работы таких твердых сплавов при неблагоприятных условиях резания. Для первых покрытий СVD была характерна диффузия из компонентов основы в покрытие в процессе нанесения. В результате на границе твердого сплава и покрытия образовывался аморфный слой, богатый свободным углеродом, так называемая Эта-фаза, снижающая адгезию и повышающая хрупкость основы. Увеличенное округление режущей кромки несколько снижало негативный эффект, но не решало проблему. Практически полностью исключить образование Эта–фазы удалось только с внедрением модифицированного процесса СVD, когда нанесение первого слоя покрытия начинается при пониженных до 700 0С температурах. При таких температурах не возникает условий для диффузии компонентов основы и покрытия, а вырастающий слой карбида титана TiC получает структуру в виде узких вертикальных кристаллов, хорошо сопротивляющихся сдвигу. Данный процесс получил название MT-CVD, и с середины 90-х годов используется всеми ведущими мировыми производителями твердосплавных пластин. Адгезия MT-CVD покрытий значительно выше. Для них не характерен такой вид износа как отслоение покрытия.
Еще одно важное улучшение свойств твердых сплавов с покрытиями было достигнуто не за счет внедрения технологии градиентного спекания, а за счет изменения поверхностных свойств режущего материала еще до нанесения износостойкого покрытия. Благодаря этой специальной технологии при спекании можно создать на поверхности пластины слой толщиной 10–20 мкм богатый кобальтовой связкой и основным карбидом вольфрама. Этот слой отличается повышенной прочностью. Его цель – задержать распространение трещин, которые зарождаются на поверхности весьма хрупкого износостойкого покрытия, и тем самым воспрепятствовать сколам и усталостному разрушению режущей кромки при знакопеременных нагрузках. Совместное применение MT-CVD и градиентного спекания позволяет создавать многослойные износостойкие покрытия с хорошей адгезией и наращивать суммарную толщину слоев до 22–25 мкм.
Интересным, но не получившим широкого распространения технологическим новшеством стало создание фирмой Sandvik Coromant композиционно-многослойного покрытия TiN-TiN/Al2O3-TiCN для пластин серии GC 2025, в котором слой TiN/Al2O3 состоит из субслоев наноразмерной толщины с нанокристаллическими зернами. Пластины GC 2025 показывали стойкость до 2–2,5 раз выше стойкости пластин со стандартным многослойным покрытием при обработке вязких материалов, как аустенитные нержавеющие стали. Но тем не менее были найдены и более эффективные методы повышения свойств MT-CVD покрытий, не требующие создания многослойных наноструктур.
На рисунке показан разрез типовой структуры твердого сплава по технологии МТ-CVD.
Пластины данного типа являются в настоящий момент индустриальным стандартом. Технология доступна не только ведущим мировым и отечественным производителям инструмента, но ее освоили и их молодые конкуренты из Кореи и Китая.
Для выживания в конкурентной борьбе необходимо дальнейшее улучшение свойств покрытий. Основное направление этих улучшений – повышение надежности работы пластин для создания условий полностью безлюдной эксплуатации металлорежущего оборудования.
Относительно недавно был найден еще один способ усовершенствования CVD покрытий. Как уже говорилось ранее, трещины из износостойкого покрытия могут проникать в твердый сплав. Основной причиной образования трещин на поверхности покрытия является разница температурных коэффициентов линейного расширения основы и покрытия. При остывании пластина сжимается меньше, чем покрытие, и соответственно покрытие покрывается сетью нанотрещин. В оставшихся целыми участках покрытия сохраняются остаточные растягивающие напряжения, а такие напряжения в поверхностном слое любого изделия, в том числе и твердосплавной пластины – это потенциальная опасность появления новых трещин и усталостного разрушения при воздействием знакопеременных нагрузок. Способ борьбы с этим явлением поражает своей парадоксальностью: если известно, что растягивающие напряжения концентрируются в верхних слоях покрытия, то давайте сделаем его излишне толстым, а затем эти слои удалим.
Простая идея потребовала кропотливой технологической работы. Но в результате с разбросом в 1–2 года многие ведущие производители вывели на рынок пластины, где верхние слои покрытия удалены одним из способов абразивной полировки. Вместе с удаленной с поверхности пластины частью слоя оксида алюминия уходят до 80% остаточных напряжений. Полированная поверхность слоя Al2O3 также оказывает благоприятное воздействие на процесс резания, так как снижается трение и передача тепла в пластину.
Первыми пластинами, где новая концепция была показана со всей очевидностью, стала серия сплавов для обработки чугуна Tiger-Tec, представленная компанией Walter. Эти пластины сразу выделялись на фоне конкурентов, поскольку были единственными обладавшими двухцветной окраской: традиционный желтый цвет TiN на задней поверхности на фоне блестящей черной передней поверхности полированного оксида алюминия. Эта же технология представлена была ведущими фирмами в различных вариациях: Sandvik Coromant – полировка передней поверхности, Iscar – полировка передней и части задней поверхности, Mitsubishi – полировка задней поверхности. Сплавы с пониженным уровнем внутренних напряжений в покрытиях MT-CVD могут быть созданы для работы в широком диапазоне скоростей резания от 80 до 400 м/мин. Очевидно, что резерв совершенствования свойств покрытий за счет новой технологии еще не исчерпан. Сейчас пионеры данного направления разработали и вывели на рынок уже второе поколение подобных сплавов.
В будущем можно ожидать разработки СVD покрытий, содержащих слой оксида циркония ZrO2. Опыты показывают, что этот материал может препятствовать диффузии компонентов твердого слава в обрабатываемый материал при высоких температурах в 26 раз более эффективно, чем оксид алюминия. Кристаллическая форма оксида циркония обладает высокой твердостью и также является абразивным материалом. Но пока не удается получить этот оксид в кристаллической форме для покрытий.
Совершенствование PVD покрытий
Как уже говорилось, покрытия PVD появились позже, чем CVD, но основное развитие происходило одновременно. Покрытия PVD свободны от свойственных CVD недостатков. Они обладают хорошей адгезией, не влияют на прочность основного инструментального материала и даже создают благоприятные сжимающие напряжения в поверхностном слое. Кроме того, для PVD покрытий всегда существовала незанятая рыночная ниша повышения режущих свойств концевого, мелкоразмерного инструмента, как твердосплавного так и из быстрорежущих сталей. Эволюция PVD идёт, в основном, по пути поиска комбинаций покрытий, обеспечивающих большую износостойкость. Благодаря успехам, достигнутым в этом направлении, покрытия PVD отвоевали у CVD по разным оценкам от 30 до 40% рынка твердосплавных пластин. Повышение размерной стойкости профильного и размерного инструмента является основным преимуществом, поскольку часто такие покрытия наносятся на мелкоразмерный инструмент, где получить выигрыш от увеличения скоростей резания не представляется возможным по причине технологических ограничений по скорости вращения шпинделя или подачи металлорежущего оборудования. Там, где скорость резания не ограничена технологией, например для токарных и фрезерных пластин, PVD сплавы могут устойчиво работать на скоростях 200–250 м/мин.
Более высокие скорости резания характерны для случаев высокоскоростного фрезерования, но следует понимать, что в этом случае значения 500 м/мин и даже до 1000 м/мин могут быть достигнуты не за счет уникальных свойств покрытия, а в основном за счет выбора специфических стратегий фрезерования, когда время реального контакта режущей кромки с обрабатаваемым материалом сокращается до миллисекунд.
Простейшие однослойные PVD покрытия TiN сейчас применяются для метчиков и быстрорежущих фрез средней производительности, используемых для обработки простых материалов на низких скоростях. Эти же покрытия можно увидеть на сверлах из быстрореза, предлагаемых для домашнего использования.
В серьезных индустриальных применениях тербуются более теплостойкие покрытия. Однослойное покрытие ТiCN продолжает использоваться для быстрорежущих и твердосплавных фрез общего назначения. Оно обладает высокой абразивной износостойкостью. Однако оно повсеместно вытесняется еще более производительным покрытием со структурой титан-алюминий нитрид TiNAl.
На протяжении последних десятилетий во всем мире наблюдается значительный рост потребления режущего инструмента в авиационной промышленности, где наиболее сложными материалами для обработки являются титан и жаропрочные сплавы. Для этих материалов характерно очень высокое контактное давление в зоне вершины режущей кромки, вызывающее разрушение и отслоение обычных однослойнвых покрытий и приводящее к усталостному разрушению основного инструментального материала. Скорости резания, достижимые при обработке титана, не превышают 50 м/мин, а для жаропрочных сплавов снижаются и до 20 м/мин даже при использовании твердосплавных инструментов.
Наноструктурированные покрытия
В условиях высоких нагрузок на режущую кромку большие преимущества при производстве режущего инструмента обеспечивают наноструктурированные покрытия. Ультрадисперсные материалы с увеличенной площадью межзеренных границ имеют более сбалансированное соотношение между твердостью, оказывающей определяющее положительное влияние на износостойкость и прочностными характеристиками материала, в том числе и в условиях действия циклических термомеханических напряжений. Известно, что первопричиной разрушения материалов стандартной (микрометрической) структуры с размерами зерен свыше d > 1 мкм является формирование трещин, возникающих вследствие концентрации дислокаций у различных дефектов. В наноструктурированных материалах с размерами зерен менее d < 80…100 нм проявляется иной механизм разрушения. Для подобных материалов превалирующей причиной разрушения являются процессы на межзеренных границах, что связано с меньшим или сравнимым количеством атомов в зернах по сравнению с их количеством на границах. Материал покрытия в наноразмерных зернах практически идеален. Разрушения зерен вследствие дислокаций практически не встречаются, а если они и происходят, то они быстро и эффективно тормзятся на границах зерен. В наноматериалах наблюдается препятствование ветвлению и движению трещин вследствие упрочнения границ зерен.
(Ti, Al)N
Ведущие разработчики покрытий для режущего инструмента, получаемых методами физического осаждения PVD (Balzers, Cemicon, Metaplas, Leybold, Platit и др.), разработали гамму наноструктурированных покрытий для нанесения на режущие инструменты, которые предлагаются потребителям для широкого применения. Наибольшее распространение пока получили покрытия (Ti, Al)N, где нанослои нитридов титана и алюминия постоянно меняются местами, создавая градиент концентрации составных элементов. Такие покрытия называют наноградиентными.
Фирма Platit (Швейцария) разработала двухфазные наноструктурированные покрытия с размерами зерен до 5 нм, у которых основную функцию по износостойкости выполняют зерна (Al,Cr)N или (Ti,Al)N (основная нанокристаллическая фаза) на границах которых располагается вторая нанокристаллическая (или аморфная) фаза Si3N4, сдерживающая коагуляцию зерен основной фазы как при осаждении покрытия (вакуумно-дуговая технология), так и при эксплуатации инструмента. Аналогичные исследования по разработке наноструктурированных покрытий нового поколения проводят фирмы Balzers, Metaplas, Cimicon и др.
Таким образом, создание покрытий для режущего инструмента нового поколения наиболее эффективно осуществлять при использовании инновационной концепции многослойно-композиционных архитектуры с нанометрической структурой и чередующимися слоями наноразмерной толщины различного композиционного состава и функционального назначения. Одним из направлений совершенствования покрытий PVD является создание комбинаций структур позволяющих использовать концевой и размерный инструмент для работы без СОЖ. Для твердосплавных пластин эта задача успешно решается за счет использования покрытий MT-CVD, работающих на высоких скоростях резания далеко за пределом наростообразования. В случае концевого инструмента достижение эффекта невозможно. Поэтому приходится решать задачу иными методами, включая в структуру PVD из аморфных материалов, выполняющих роль смазки.
Покрытия DLC (Diamond Like Coatings)
Принципиально отличными от вышеописанных, но также относящихся к классу PVD, являются покрытия DLC (Diamond Like Coatings). Получаемые при этом углеродные нанопленки близки по свойствам к алмазу. Такие покрытия обладают очень высокой, превосходящей до 50 раз другие типы покрытий абразивной износостойкостью. К сожалению, их температурная стабильность и стойкость к окислению ограничены величиной 300 0С, что недостаточно для большинства случаев металлообработки, за исключением резания алюминия и силумина. Но, благодаря своей абразивной стойкости покрытия, DLC показывают хорошие результаты при обработке резанием различных композиционных материалов на основе стекло- и угле- наполненных пластиков, находящих все более широкое применение в технике.
В 2005 году фирма Walter впервые заявила о создании промышленной технологии нанесения PVD покрытий, содержащих слой оксид алюминия. Эти покрытия должны сочетать достоинства PVD покрытий с износостойкостью CVD, где оксид алюминия выполняет основную защитную функцию. Выпущенная гамма сплавов предлагается для обработки труднообрабатываемых материалов, таких как жаропрочные сплавы, и имеет хороший коммерческий успех, однако странно, что распространения этой технологии на другие твердые сплавы пока нет ни в производственной программе Walter, ни у других компаний.
Китай и распространение технологий
Установки CVD достаточно громоздки и занимают от 50 м2 производственной площади и более, и имеют сложную систему подвода газов. Некоторые газы, используемые для инструментальных CVD покрытий, токсичны, поэтому требуется соблюдение строгих мер безопасности. С момента появления технология CVD остается дорогим удовольствием, доступным только специализированным инструментальным предприятиям производящих твердосплавную продукцию по полному циклу в массовом масштабе и способных позволить себе создание собственных CVD-установок. Для случаев мелкосерийного изготовления специального инструмента или для восстановления небольших партий переточенного инструмента данная технология не применима.
Технология покрытия PVD доступна. Небольшие инструментальные производства, инструментальные цеха больших предприятий могут себе позволить приобрести один из вариантов PVD-установок, которые активно продвигаются на рынке всеми ведущими компаниями, работающими над созданием покрытий Balzers, Cemicon, Metaplas, Leybold, Platit.
Этим объясняется факт наличия очень жесткой ценовой конкуренции как на рынке нового концевого инструмента, так и на переточке твердосплавного инструмента. В сложившейся рыночной ситуации самые современные наноструктурированные покрытия стали доступны не только первой линейке ведущих инструментальных компаний, но и вторым брендам и небольшим производителям. Не удивительно, что все более конкурентные предложения появляются от китайских компаний инструмента, вкладывающих огромные деньги в закупку современного оборудования по нанесению износостойких покрытий.
Россия
А что же Россия? Удивительно, что с момента появления технология PVD активно развивается при участии различных групп российских ученых, но плоды этого развития в основном реализуются западными компаниями. Несмотря на то, что в нашей стране активно действует немало лабораторных установок, способных производить покрытия PVD, соответствующие лучшим мировым образцам, их внедрение в практику отечественной инструментальной промышленности не происходит.
Автор: Максимов Михаил
Иллюстрации с сайта Sandvik Coromant
- Войдите на сайт для отправки комментариев
Только что вышел материал: «РОСНАНО начинает оправдывать смысл своего существования» о предприятиях которые софинансирует РОСНАНО и которые начнут выпуск своей продукции уже в 2010году. Среди них упоминается завод в Рыбинске по производству металлорежущего инструмента с износостойким нанопокрытием.